A virtue out of necessity
Craftsmanship meets innovation: At TRILAY, we are convinced that 3D printing of orthopedic insoles is the future of the OST industry. That's why we're doing everything we can not only to keep improving the quality of new technologies, but also to make them accessible and easy to use for businesses of all sizes.
The enthusiasm for insole printing began rather unspectacularly. Back in 2016, company founder and CEO Christian Tausch asked himself whether 3D printing, which was emerging at the time, could be something for the professional production of orthopedic insoles. At the time, however, he came to the conclusion that the technology was not yet mature enough to meet the high demands of the industry.
Sometimes an idea just needs time to mature. When the Corona pandemic caused material supply bottlenecks in 2020, Tausch took his ideas out of the drawer again. 3D printing had evolved in the meantime. At the same time, the desire to be able to produce in a more material-saving and energy-efficient way was becoming increasingly urgent.
The best of two worlds
Despite all the expertise in the shoemaking trade and decades of experience in the supply of insoles, it quickly became clear that the company could not go it alone. After all, highly specialized materials and sophisticated printing processes are needed if the focus is not only on the highest quality but also on the cost-effectiveness of printed insoles.
At the same time, Dominic Ring was looking at ways to apply 3D printing in various industries. During a visit to Tausch's workshop in Ammerbuch, it became clear to him that things are not done by halves here, but are tackled properly. In other words, it's exactly the kind of working atmosphere that inspires and motivates the innovative industrial engineer and mechanical engineer. The two decided to work together to find solutions for insole supply.
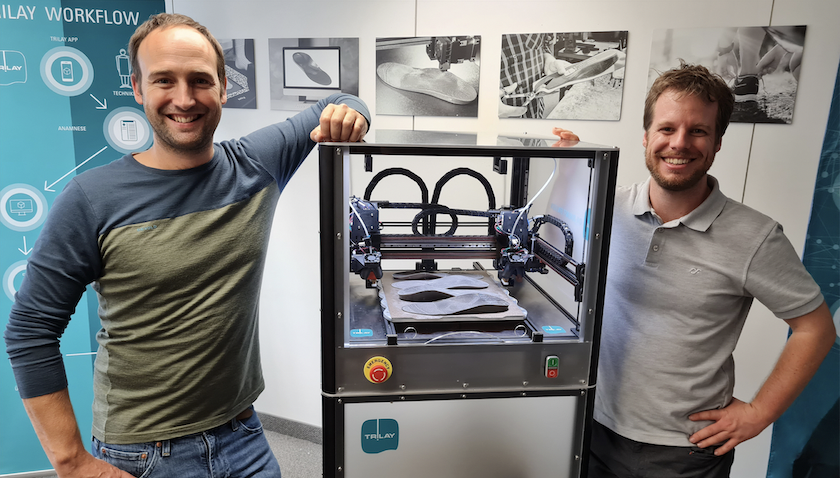
The collaboration quickly bore its first fruits, but was also marked by challenges. Tausch had hoped that there was already a printer on the market that could meet his requirements. But Ring was certain that the best solution would be a special printer that was precisely tailored to the requirements of orthopedic shoemakers.
Initially, Tausch tested a prototype in his own workshop. But it took less than two weeks before he requested a second printer - despite minor optimization possibilities, the device exceeded all expectations. The experience gained from the first test runs was incorporated into the next iteration, so that this device was already producing at the highest level. In 2022, the two founded TRILAY to partner in advancing the vision of premium insoles from the 3D printer. Since then, Tausch and Ring have been continuously developing the printing process. Today, they achieve excellent results through specialized equipment, optimal material composition and sophisticated process optimization.
Committed to the future
At TRILAY, we see long-term effective solutions as our mission. This starts with material-saving, efficient processes. This saves costs for production, disposal and storage. Environmental impact is minimized. In addition, it is important to us to contribute to the job quality of skilled workers. They are exposed to less dust and noise through 3D printing, so their health is protected more sustainably than through previous processes. The fact that there is also more time for other work, in particular for consultation, contributes to lasting patient satisfaction and a better care situation.
Last but not least, we want to offer our customers lasting, practicable solutions by creating customized offerings. After all, through long-lasting and at the same time flexible approaches, companies also benefit from progress in the industry in the long term.
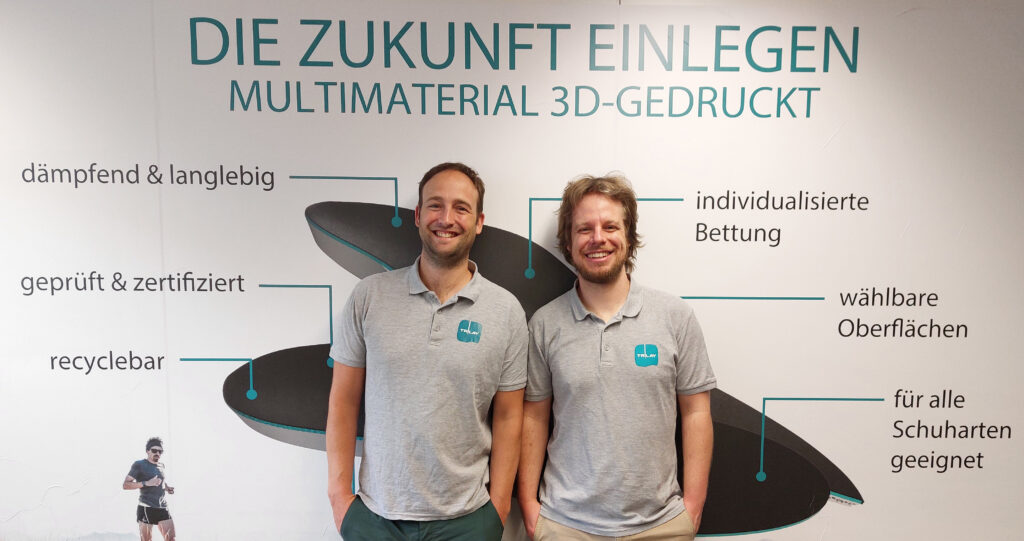
