Formvollendet: Die Zukunft 3D-gedruckter Einlagen im Handwerk
Der 3D-Druck in der Orthopädieschuhtechnik entwickelt sich rasant. Kein Wunder, schließlich versprechen orthopädische Einlagen aus dem Drucker geringen Aufwand, optimale Materialnutzung und perfekte Passform. Oft ist es gar nicht so leicht, bei all den technischen Neuerungen auf dem aktuellen Stand zu bleiben. Und natürlich stellt sich die Frage, ob gedruckte Einlagen wirklich schon mit konventionellen Herstellungsverfahren mithalten können.
Christian Tausch (links im Bild) und Dominic Ring (rechts im Bild) sind sich sicher: Gedruckte orthopädische Maßeinlagen sind die Zukunft des Handwerks und lohnen sich schon heute. Seit drei Jahren tüftelt das Duo – in der heimischen Werkstatt scherzhaft als „Team-Düsentrieb“ bekannt – an Druckern, Verfahren und Materialien, die höchste Qualität liefern und zugleich Betriebe entlasten sollen. Im Gespräch erläutern der Orthopädieschuhmacher-Meister und der Maschinenbauingenieur, was sie herausgefunden haben und worauf man beim Einstieg achten sollte.
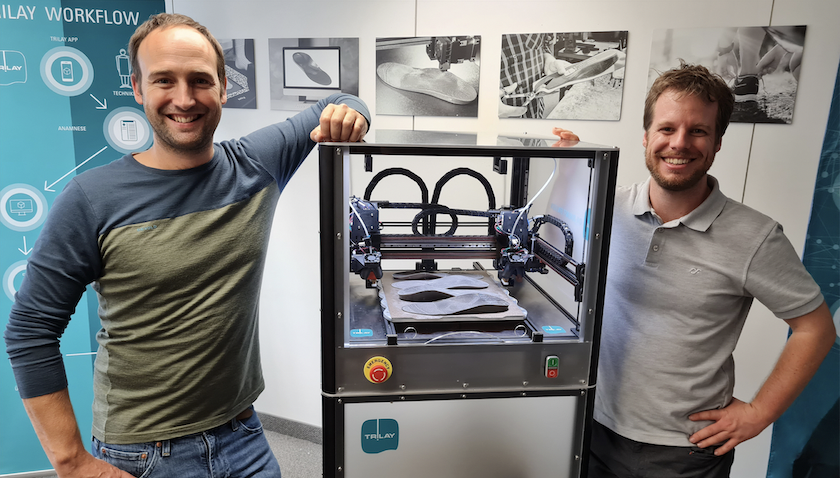
Das Wichtigste zuerst: Orthopädische Einlagen drucken – ist das überhaupt schon in ausreichend hoher Qualität möglich?
CT: Das ist auf jeden Fall möglich! Mit dem nötigen Know-How, der entsprechenden Technik und erprobten Materialien hält der FDM-Druck (Fused Deposition Modelling) heute gut mit den konventionellen Herstellungsverfahren mit. Am Anfang konnten wir kaum glauben, was für eine hohe Qualität wir in punkto Langlebigkeit und Wirkungsweise erreichen konnten. Locker vergleichbar mit den Ergebnissen der bisherigen Verfahren! Inzwischen hat sich herausgestellt: Die ersten guten Erfahrungen waren kein Zufall, wir können mit FDM-Druck wirklich zuverlässig erstklassige Qualität schaffen. Das spiegelt sich auch im Feedback unserer Kunden wider.
FDM-Druck, das ist der so genannte „Würsteldruck“, oder? Ist der qualitativ nicht schlechter als beispielsweise der Resin-Druck?
DR: Also „Würsteldrucker“ sagt heutzutage eigentlich niemand mehr (lacht). Vor einigen Jahren, als der 3D-Druck insgesamt noch in den Kinderschuhen steckte, gab es da ein paar Herausforderungen. Inzwischen sind die aber überwunden.
Wir machen sehr gute Erfahrungen mit FDM-Druckergebnissen. Beispielsweise können wir mit diesem Verfahren verschiedene Druckmaterialien hervorragend miteinander kombinieren. Auch unsere Kunden und Messebesucher bestätigen uns immer wieder, dass die gedruckten Einlagen sich hervorragend weiterbearbeiten lassen und tolle Qualität haben.
Das klingt interessant. Man kann also bereits verschiedene Shore-Härten miteinander kombinieren?
DR: Ja, absolut! Wir drucken von steinhart bis superweich alles in eine Einlage und erreichen damit vielseitige funktionelle Eigenschaften. Stabil, bettend, Schaleneinlagen, Rigidusfedern… wir kriegen inzwischen vieles hin.
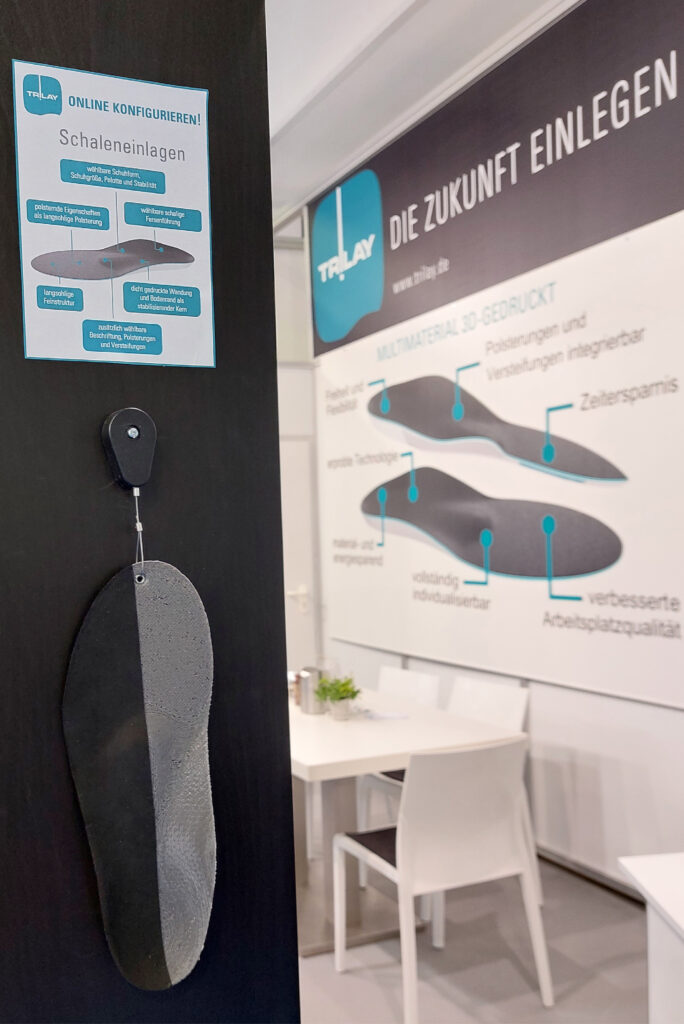
Aber läuft man bei der Kombination verschiedener Materialien nicht Gefahr, dass die Stabilität der Einlage leidet, sie im schlimmsten Fall regelrecht auseinanderfällt?
CT: Nicht mit dem richtigen Druckverfahren. Wir wissen inzwischen sehr genau, wie wir Materialien unterschiedlicher Härtegrade kombinieren und zuverlässig miteinander verbinden können. Für die Herstellung von orthopädischen Einlagen ist es zentral, dass wir die Materialeigenschaften präzise einsetzen können. Nur so können wir Versteifungen und Entlastungen direkt im Druck ermöglichen, die Individualität und den medizinischen Nutzen gewährleisten, und natürlich auch dem Hilfsmittelkatalog entsprechend produzieren. So ein Fersensporn-Polster beispielsweise entlastet nur dann optimal, wenn es die richtigen Dämpfungseigenschaften hat und an der richtigen Position sitzt.
Klingt gut, ist aber nicht ganz leicht vorstellbar. Wie funktioniert das denn?
DR: Da kann man über die Druckstrategie viel erreichen – bis zu einem gewissen Grad. Um die Bandbreite der Eigenschaften darüber hinaus zu erweitern, haben wir hier gezielt weitere Materialen getestet und Kombinationsmöglichkeiten systematisch erprobt. Daher wissen wir, welches Material am besten für eine bestimmte Eigenschaft geeignet ist.
Stichwort orthopädische Einlagen – da muss das Druckmaterial ja speziell zertifiziert werden. Ist das nicht teuer und aufwendig?
DR: Guter Punkt. Schlechte Filamentqualität ist tatsächlich der größte Gegner von guten Drucken. Deshalb haben wir uns in der Entwicklung unseres Angebots viel Zeit genommen, um das optimale Material für orthopädische Einlagen anbieten zu können. Das TRILAY SL Filament ist nicht nur zertifiziert, sondern ist auch ein High Speed TPU Filament. Damit lassen sich sehr hohe Druckgeschwindigkeiten realisieren.
CT: Genau, eine hohe Bandbreite an Farben können wir auch anbieten. Das ist ja fürs Branding der Betriebe von Bedeutung. Auch Logos können problemlos aufgedruckt werden. Noch wichtiger ist aber, dass die entfernungsresistente Beschriftung eine vollständige, MDR-konforme Dokumentation ermöglicht. Das erleichtert den Arbeitsalltag enorm.
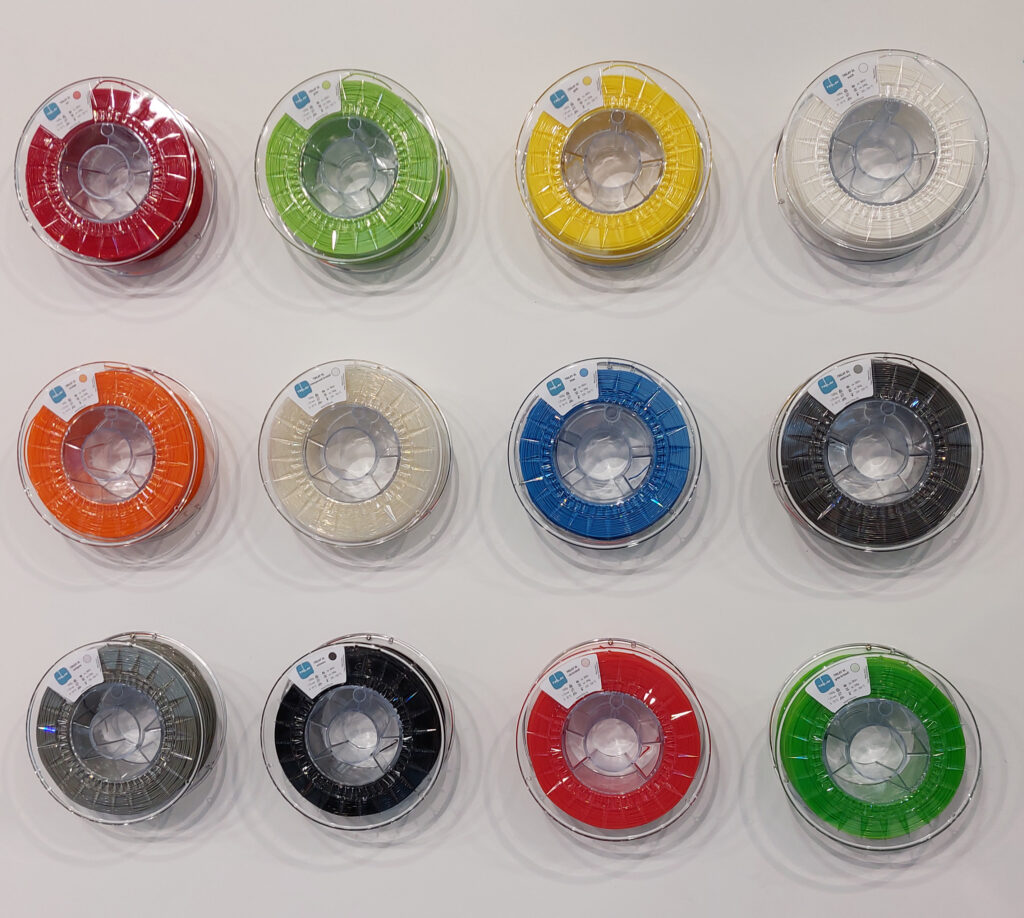
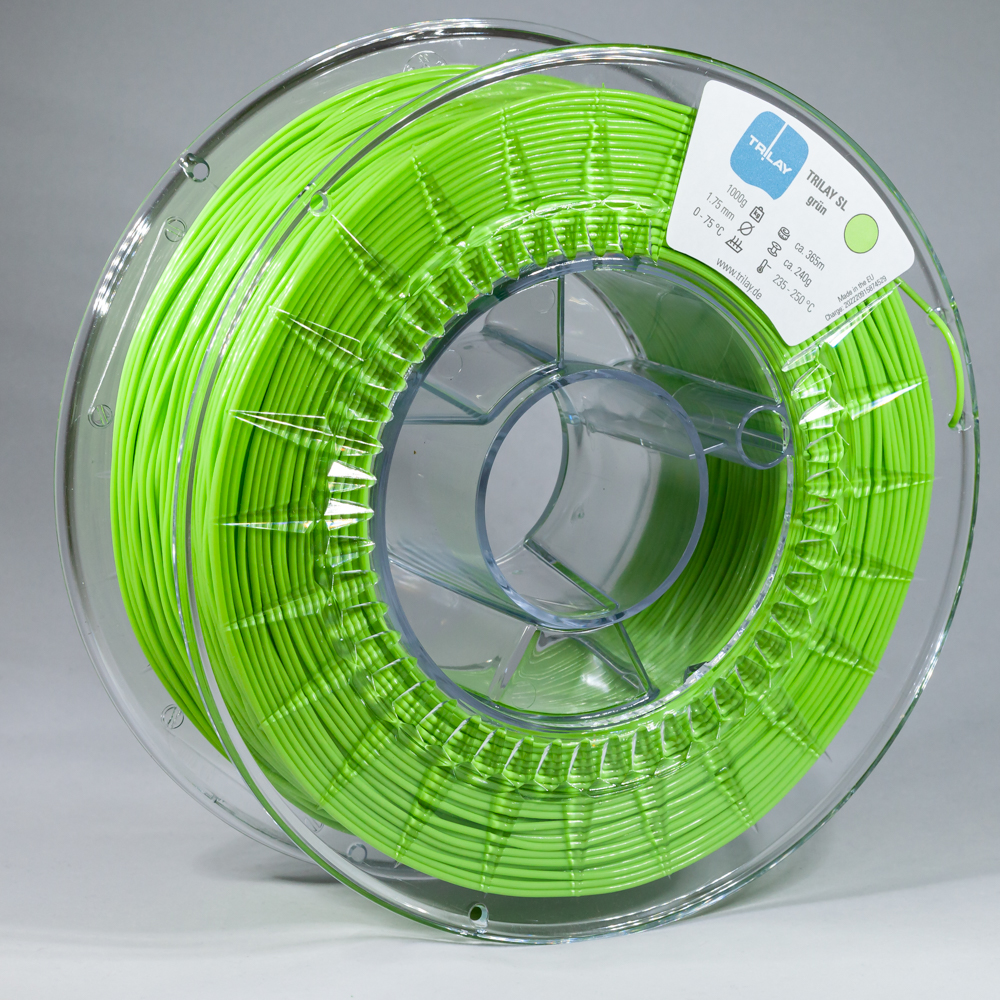
Aber lohnt sich 3D-Druck denn? Materialien und Energie sind ja nicht gerade billig.
CT: Der Umstieg lohnt sich durchaus. Wir haben daran gearbeitet, die Druckzeit massiv zu reduzieren und konnten z. B. auch das Vorheizen optimieren. Das verringert Energieaufwände und Wartezeiten. Ein großer Vorteil ist natürlich, dass quasi kein Verschnitt entsteht. Das spart nicht nur Geld, sondern entlastet auch die Umwelt. Alte Einlagen können zudem recycelt werden.
DR: Um das Ganze mal in Zahlen auszudrücken… ein 3D-Drucker, der den ganzen Tag Einlagen produziert, benötigt im Schnitt knapp unter 2kWh pro Tag. Vergleicht man das mit dem Energieaufwand einer herkömmlich gefrästen Einlage, liegt die Einsparung bei ca. 20 %. Noch zum Thema Verschnitt: Beim Fräsen beispielsweise entstehen ca. 80 % Abfall und man muss ein großes Rohlinglager vorhalten. Beim 3D-Druck fallen diese Nachteile einfach weg.
CT: Richtig. Außerdem muss beim TRILAY-Verfahren nur minimal nachbearbeitet werden. In den meisten Fällen einfach anrauen, beziehen, fertig. Je nach Anforderung kann die Einlage bei unvorhersehbaren Änderungen aber auch wie gewohnt geschliffen und verklebt werden. Die Arbeitszeit hochqualifizierter Mitarbeiter kann effektiver genutzt werden, das muss man in der Kalkulation ja auch berücksichtigen.
Beim Resin-Druck ist das übrigens anders, da sind in der Tat noch einige Schritte nach dem Druck nötig, bis die Einlage wirklich fertig ist. Noch dazu unter Einsatz von Chemikalien und speziellen Werkzeugen. Klarer Vorteil für den FDM-Druck, würde ich sagen.
Insgesamt dürften die meisten Betriebe mit dem passenden 3D-Druck-Prozess also besonders kostengünstig produzieren.
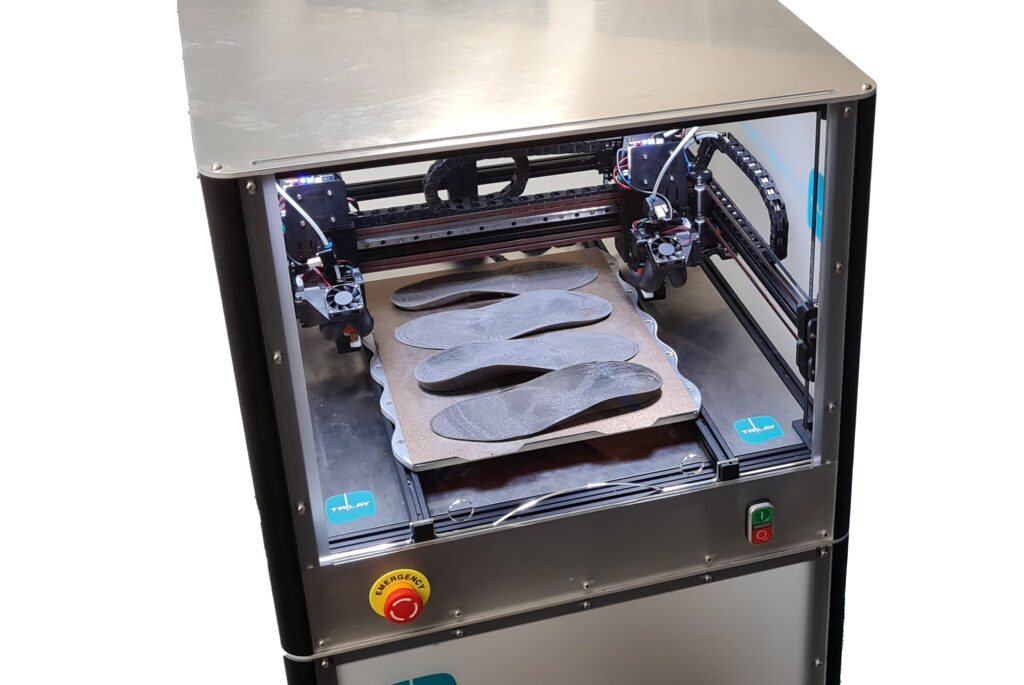
Bleibt allerdings noch der Drucker, auch der kostet in der Anschaffung.
CT: Klar, aber um den Einstieg zu erleichtern bieten wir verschiedene Modelle an. Von Druckservice über Kapazitätsmiete bis zum Kauf bieten wir viele Möglichkeiten an. So wollen wir sicherstellen, dass Betriebe aller Größen Zugang zur 3D-Druck Technologie bekommen.
DR: Man muss auch keine Software dazukaufen. Der einfachste Zugang ist bei uns kostenlos, den kann man einfach beantragen und im Webshop loslegen.
Viele Orthopädieschuhmacher dürften der Sache skeptisch gegenüberstehen. Müssen sich Handwerker sorgen machen, ersetzt zu werden?
CT: Nein, auf keinen Fall. Ich bin selbst schon lange Orthopädieschuhmacher-Meister, kenne das Handwerk von klein auf und versuche auch, die Familientradition meinen Kindern offen zu halten. Handwerk ist für mich Herzenssache. Die Fachkräfte werden definitiv auch zukünftig gebraucht, ohne die geht gar nichts. Ihre Erfahrung und ihr Know-How sind unabdingbar, um die Versorgungsqualität zu sichern. Ohne Fachkräfte könnten die hohen Anforderungen gar nicht erfüllt werden.
DR: Uns ist es deshalb wichtig, die Belegschaft mitzunehmen, wenn ein Unternehmen den 3D-Druck einführt. Da muss man dann individuell hinschauen, was gebraucht wird. Da beraten und unterstützen wir sehr gern. Unsere Erfahrung zeigt aber, dass nach einer kurzen Umstellungsphase auch die Mitarbeiter von der Technologie profitieren. Schließlich steigt die Arbeitsplatzqualität, wenn weniger gefräst wird: Geringere Staub- und Lärmbelastung sind nicht nur angenehmer, sondern auch schlichtweg gesünder. Außerdem macht es vielen Spaß, Neues zu lernen, fortschrittlich zu arbeiten und beispielsweise auch mehr Zeit für die Beratung zu haben.
Und wie kann man mehr über die Möglichkeiten 3D-gedruckter Einlagen erfahren?
CT: Am liebsten sprechen wir direkt mit Interessenten. Wir nehmen uns gern die Zeit, unsere Produkte zu präsentieren, zusammen den Online-Einlagenkonfigurator zu testen, alle Fragen zu beantworten, und eventuelle Bedenken auszuräumen. Auf Fachmessen freuen wir uns immer über einen Besuch und auf unserer Homepage können Sie jederzeit einen persönlichen Termin vereinbaren.
Oft wird einem dann erst bewusst, dass der Einstieg viel einfacher ist als zuerst gedacht.
Interviewer: Verena Pachler